Extrusión Industrial
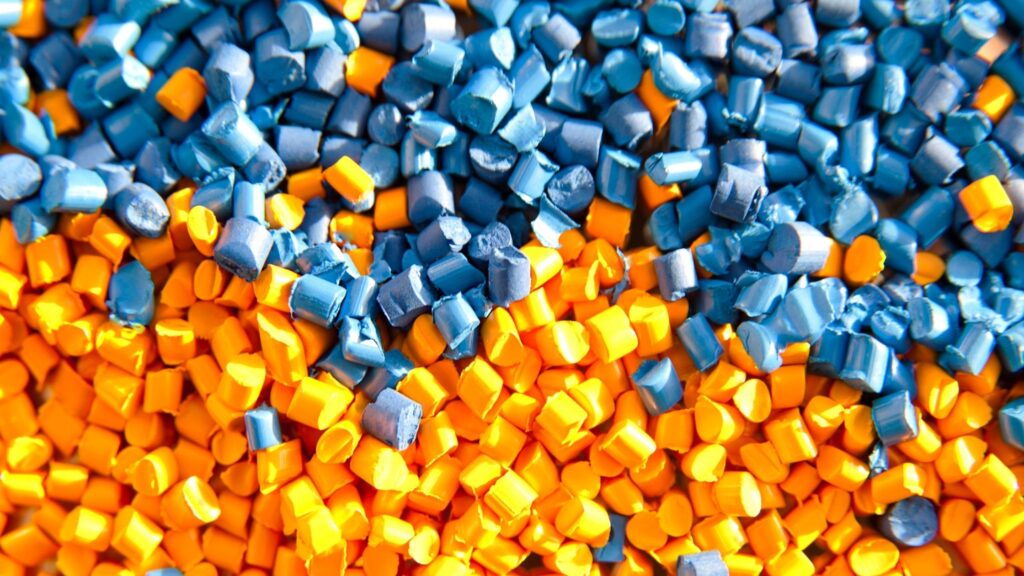
El proceso de extrusión en la industria es ampliamente utilizado para la manufactura de materiales plásticos y metálicos en su mayoría para la fabricación de estructuras en la construcción, arquitectura, decoración, Diseños y desarrollos de ingeniería así como artículos y herramientas en nuestra vida cotidiana.
Para lograr este objetivo se requieren de máquinas cuyo diseño en general requiere de un sistema de calentamiento y/o control de temperatura a la cual el material se va a destruir o manipular, este parámetro es muy importante ya que de no contar con los equipos periféricos adecuados la calidad del producto puede verse afectada desde provocar merma hasta problemas o errores en control de calidad.
- Mantenimiento requerido cada 6 meses a 1 año dependiendo calidad del agua de enfriamiento.
- No requiere personal especializado para el mantenimiento ni mucho personal para realizarlo.
- Tiempos de paro cortos.
- Eficiencia de enfriamiento recuperable hasta un 90%.
- No requiere maniobras adicionales o desmontaje para limpieza de placas y empaques.
- Alta disponibilidad en refacciones y equipos nuevos
Algunas aplicaciones e industrias donde se encuentran operando con gran eficiencia son:
- Extrusión de filamento plástico
- Extrusión de perfiles de aluminio
- Peletizadoras
- Fabricación de tubos metálicos y plásticos
- Manufactura de termoplásticos
- Enfriamiento de sistemas hidráulicos de máquinas extrusoras
- Control de temperatura en diferentes zonas de Banburies
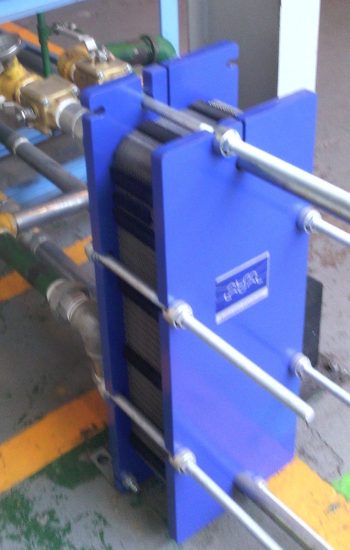
Con uno de nuestros clientes hemos logrado ayudarle a reducir los tiempos de mantenimiento en una máquina de inyección plástica tiene un depósito de aceite el cual debe mantenerse a una temperatura de 40-45ºC para el correcto funcionamiento del sistema hidráulico.
¿El problema? Se tenían instalados intercambiadores de calor de tubo y coraza en serie para poder enfriar con agua de chiller y apenas mantener la temperatura en 50ºC, lo que ocasiona degradación en el aceite y problemas de calentamiento en algunas partes de la máquina. Además, el tiempo de mantenimiento que requería cada intercambiador era de 2-3 días hábiles y 2 personas en planta, así como herramienta especial.
La solución: Se seleccionó un intercambiador de calor de placas con base a la capacidad de la máquina y suministros de agua de enfriamiento disponible en planta. Actualmente, el equipo lleva 2 años operando en un rango entre 40-45ºC con agua de chiller, no ha requerido mantenimiento, sin embargo, este año en curso se le hará un preventivo solamente para confirmar el estado interno del equipo.
Equipo seleccionado: Intercambiador de calor de placas Alfa Laval modelo M6M.
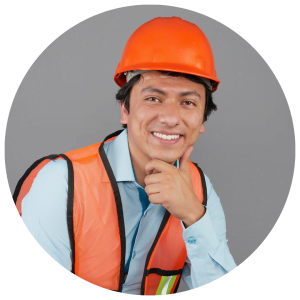
Moisés Morales Hernández
Especialista en intercambio de calor